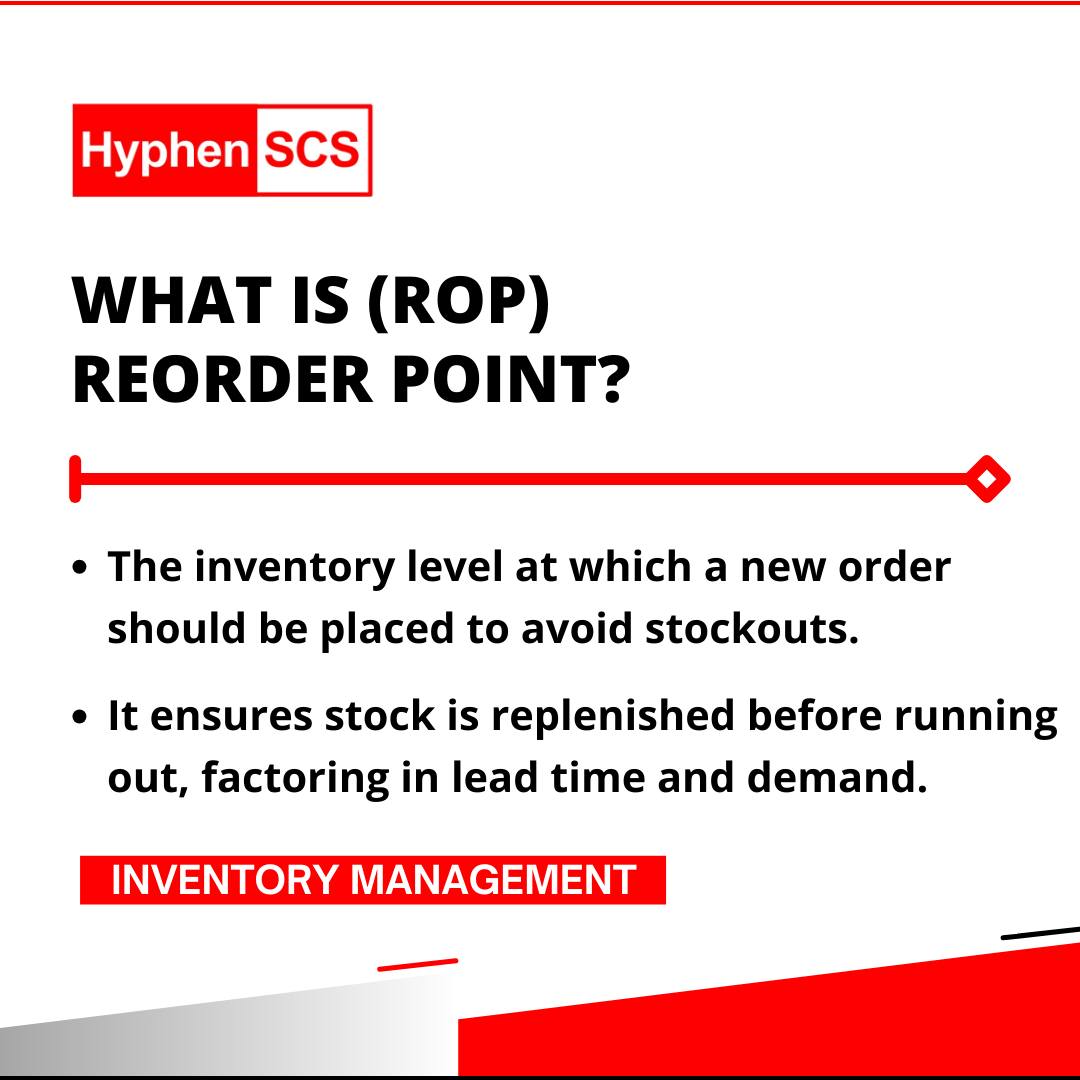
What is the Reorder Point (ROP) in Inventory Management?
In the world of warehousing, Reorder Point (ROP) is a critical concept every professional should understand. ROP refers to the inventory level at which a new order should be placed to prevent stockouts. It's like your inventory safety net, ensuring you never run out of stock.
How does it work?
ROP factors in two essential elements:
Lead Time: The time it takes for new stock to arrive after placing an order.
Demand: The rate at which products are sold or used.
By calculating the ROP, businesses can make informed decisions about when to reorder, preventing inventory shortages and optimizing supply chain efficiency. Why itβs important:
Helps prevent stockouts and production delays
Ensures steady product availability
Improves overall inventory management
Stay tuned for more warehousing insights and technical tips!